I recently saw an electrician using a noncontact type voltage detector to verify the absence of voltage while replacing ballasts in an office building. He was standing on a ladder and waving the detector back and forth under the light. If the meter didn’t light-up or beep, he assumed the circuit was dead and then proceeded with his repair. I politely asked the young man if he had ever been trained to use the device or understood how it worked. I received the “Leave me alone. I’ve got work to do” look, and he went back to the task at hand.
I understand that noncontact voltage detectors are cheap, quick and easy to operate, but they can be dangerous if you don’t understand their limitations or use them for the incorrect purposes.
How noncontact voltage detectors work… and how they don’t
Noncontact voltage detectors, also known as proximity testers or noisy testers, do not require actual metal to metal contact in order to detect voltage. These devices work on an electrical concept known as capacitive coupling.
In effect your body becomes one of two capacitors in series with the energized part and ground. For the device to work properly, your hand must touch the plastic body of the instrument and another part of your body needs to be coupled to ground (in most cases this is through your feet.)
If for any reason, you become isolated – for instance you’re standing on a wooden ladder – the instrument will not sense voltage even though it is present.
This can lead to a very unpleasant shock, serious injury, or worse. For more information and a better understanding of the capacitive coupling concept, I strongly recommend reading Fluke’s informational pages, Understanding Capacitive Voltage Sensors and Getting the Most Out of Your Voltage Detector.
Don’t get me wrong, I do think there is a place in the electrician’s tool pouch for these devices. However, the user must understand how these tools work and their limitations. NFPA 70e® agrees with me. See article 110.2(D)(1) Training Requirements for a Qualified Person, which reads as follows:
Employees shall be trained to select an appropriate test instrument and shall demonstrate how to use a device to verify the absence of voltage, including interpreting indications provided by the device. The training shall include information that enables the employee to understand all limitations of each test instrument that might be used.
First and foremost, read the manufactures’ instructions and precautions.
I think you’ll be surprised at what you’ll learn. Make sure the category rating for the instrument is at the level required for the work you are performing. A Minimum of Cat III at 600 volts is required for industrial environments. Also, verify that it is rated for the voltage level that you are testing. Testing the instrument on a known live source, before and after using it on the equipment being tested, is an absolute must. This warning is typically printed right on the side of the instrument. Do not rely on the instrument for verifying the absence of voltage. Use a direct contact meter before touching something that is normally energized above 50 volts.
HOW to use noncontact voltage meters
If you do allow the use of noncontact voltage detectors in your facility, hold a shop brief and explain how they work. Write in your electrical safety policy when and where they can be used. It may be a good idea to purchase and supply them to your employees. Not all detectors are created equal. This will ensure that the equipment being used is of good quality and suited for the environment.
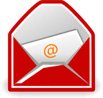
Sign up for our free weekly Safety Tips and receive one weekly, right to your inbox!